
SUSTAINABLE MODULAR SOLUTIONS TO RESIDENTIAL DEVELOPMENT
Project 1
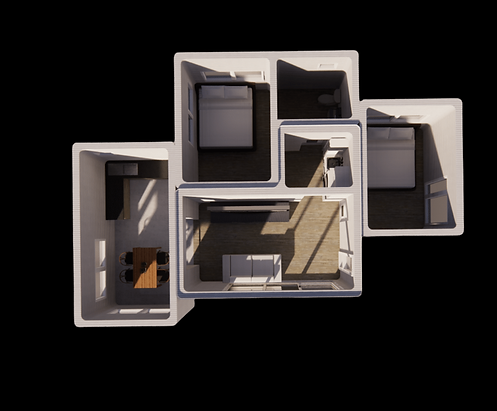
Residential projects have been one of the pivotal forms of architecture. Architects and engineers often come up with revolutionary ways to transform people's standard of living through technological advancements. However, increased housing developments has led to undesirable environmental issues as the construction industry becomes a major consumer of non-renewable resources that produces non-reusable waste. This results in proposing an idea that could introduce environmental and cost-friendly technology in housing projects, bringing sustainability and flexibility into architecture.
While software and cloud could reshape construction's digital landscape, there are two technologies poised to improve the industry's physical landscape: 3D printing and modular construction. 3D printing is not something new in building construction yet still very conceptual. Using state-of-the-art machines that ‘print’ out concrete on a base to construct its walls by layers, this cuts down time constructing a building compared to the conventional way of using contractors. Acquiring construction-grade 3D printers saves time and costs of hiring contractors. It also allows better control over inventories. The leftover materials are recycled for future projects, reducing construction waste that ends up in landfills.
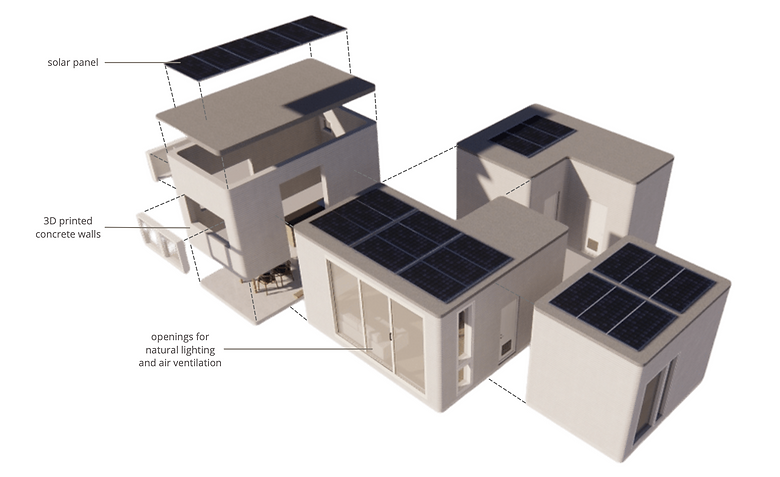

Aside from 3D printing, modular housing can be implemented with it. Modules of different spaces of the house such as the kitchens and bedrooms(Diagram1) can be premade from a facility according to site condition and clients’ bespoke preference. This greatly increases the flexibility of the building design, with different assemblage and manipulation of form(Diagram 2). The completed modules are transported and assembled on site with the help of cranes. The construction site usage will be more optimized with less heavy machinery and more movable space for workers, reducing site-disturbance. With off-site construction, clean construction can be well practiced in order to increase the green footprint.
The modular 3D printed houses can be customizable even after completion. These houses can be dismantled, relocated, and reused with minimal modification. Each module can be transported to another location with the help of cranes and transporters. This allows double waste reductions. The connecting mechanism is simple to unlatch and remove which is possible to construct multiple storeys. This method saves time, especially during urgent situations.
To summarize, 3D printed houses with better quality and adaptability are much more sustainable compared to conventional building construction, due to their flexibility and waste control. It serves as a new prototype for a repeatable system of housing that can be easily adaptable to be placed in a range of different sites and urban contexts.